Questions and Answers
1. Define Benchmarking?
Benchmarking is a systematic method by which organizations can measure themselves against the best industry practices. The essence of benchmarking is the process of borrowing ideas and adapting them to gain competitive advantage. It is a tool for continuous improvement.
2. Enumerate the steps to benchmark?
a) Decide what to benchmark
b) Understand current performance
c) Plan
d) Study others
e) Learn from the data
f) Use the findings
3. What are the types of benchmarking?
i. Internal
ii. Competitive
iii. Process
4. What is a QFD?
Quality Function Deployment is a planning tool used to fulfill customer expectations. It is a disciplined approach to product design, engineering, and production and provides in-depth evaluation of a product.
5. What are the benefits of QFD?
i. Customer driven Product/Servive design and development
ii. Reduces implementation time
iii. Promotes teamwork
iv. Provides documentation
6. What are the steps required to construct an affinity diagram?
i. Phrase the objective
ii. Record all responses
iii. Group the responses
iv. Organize groups in an affinity diagram
7. What are the parts of house of quality?
i. Customer requirements
ii. Prioritized customer requirements
iii. Technical descriptors
iv. Prioritized technical descriptors
v. Relationship between requirements and descriptors
vi. Interrelationship between technical descriptors
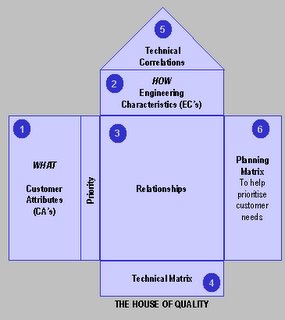
8. How will you build a house of quality?
a) List customer requirements
b) List technical descriptors
c) Develop a relationship matrix between WHATs and HOWsd) Develop an interrelationship matrix between HOWs
e) Competitive assessments
f) Develop prioritized customer requirements
g) Develop prioritized technical descriptors
9. Define FMEA?
Failure Mode Effect Analysis is an analytical technique that combines the technology and experience of people in identifying foreseeable failure modes of a product or process and planning for its elimination.
10. What are the stages of FMEA?
1. Specifying possibilities
a. Functions
b. Possible failure modes
c. Root causes
d. Effects
e. Detection/Prevention
2. Quantifying risk
a. Probability of cause
b. Severity of effect
c. Effectiveness of control to prevent cause
d. Risk priority number
3. Correcting high risk causes
a. Prioritizing work
b. Detailed action
c. Assigning action responsibility
d. Check points on completion
4. Revaluation of risk
a. Recalculation of risk priority number
11. What are the goals of TPM?
The overall goals of Total Productive Maintenance, which is an extension of TQM are
i. Maintaining and improving equipment capacity
ii. Maintaining equipment for life
iii. Using support from all areas of the operation
iv. Encouraging input from all employees
v. Using teams for continuous improvement

12. Give the seven basic steps to get an organization started toward TPM?
a) Management learns the new philosophy
b) Management promotes the new philosophy
c) Training is funded and developed for everyone in the organization
d) Areas of needed improvement are identified
e) Performance goals are formulated
f) An implementation plan is developed
g) Autonomous work groups are established
13. What are the major loss areas?
i. Planned downtime
ii. Unplanned downtime
iii. Idling and minor stoppages
iv. Slow-downs
v. Process nonconformities
vi. Scrap
14.Why is a conventional design process not sufficient?
Conventional design processes focus more on engineering capabilities and less on customer needs. When they do try to incorporate customer perspectives, these tend to be engineer-perceived or producer-perceived. Quality Function Deployment (QFD), however, focuses like a laser all product development activities on customer needs
15.How does QFD offer strategic advantage?
Regarding Taquchi,s Loss function
please follow the link for excellent intrduction given by Mr.Issa Bass SixSIgma FIrst Editor
Benchmarking is a systematic method by which organizations can measure themselves against the best industry practices. The essence of benchmarking is the process of borrowing ideas and adapting them to gain competitive advantage. It is a tool for continuous improvement.
2. Enumerate the steps to benchmark?
a) Decide what to benchmark
b) Understand current performance
c) Plan
d) Study others
e) Learn from the data
f) Use the findings
3. What are the types of benchmarking?
i. Internal
ii. Competitive
iii. Process
4. What is a QFD?
Quality Function Deployment is a planning tool used to fulfill customer expectations. It is a disciplined approach to product design, engineering, and production and provides in-depth evaluation of a product.
5. What are the benefits of QFD?
i. Customer driven Product/Servive design and development
ii. Reduces implementation time
iii. Promotes teamwork
iv. Provides documentation
6. What are the steps required to construct an affinity diagram?
i. Phrase the objective
ii. Record all responses
iii. Group the responses
iv. Organize groups in an affinity diagram
7. What are the parts of house of quality?
i. Customer requirements
ii. Prioritized customer requirements
iii. Technical descriptors
iv. Prioritized technical descriptors
v. Relationship between requirements and descriptors
vi. Interrelationship between technical descriptors
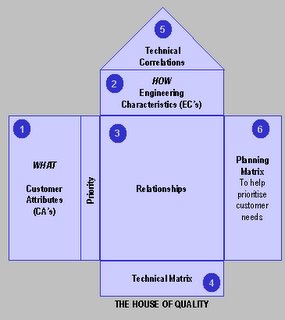
8. How will you build a house of quality?
a) List customer requirements
b) List technical descriptors
c) Develop a relationship matrix between WHATs and HOWsd) Develop an interrelationship matrix between HOWs
e) Competitive assessments
f) Develop prioritized customer requirements
g) Develop prioritized technical descriptors
9. Define FMEA?
Failure Mode Effect Analysis is an analytical technique that combines the technology and experience of people in identifying foreseeable failure modes of a product or process and planning for its elimination.
10. What are the stages of FMEA?
1. Specifying possibilities
a. Functions
b. Possible failure modes
c. Root causes
d. Effects
e. Detection/Prevention
2. Quantifying risk
a. Probability of cause
b. Severity of effect
c. Effectiveness of control to prevent cause
d. Risk priority number
3. Correcting high risk causes
a. Prioritizing work
b. Detailed action
c. Assigning action responsibility
d. Check points on completion
4. Revaluation of risk
a. Recalculation of risk priority number
11. What are the goals of TPM?
The overall goals of Total Productive Maintenance, which is an extension of TQM are
i. Maintaining and improving equipment capacity
ii. Maintaining equipment for life
iii. Using support from all areas of the operation
iv. Encouraging input from all employees
v. Using teams for continuous improvement

12. Give the seven basic steps to get an organization started toward TPM?
a) Management learns the new philosophy
b) Management promotes the new philosophy
c) Training is funded and developed for everyone in the organization
d) Areas of needed improvement are identified
e) Performance goals are formulated
f) An implementation plan is developed
g) Autonomous work groups are established
13. What are the major loss areas?
i. Planned downtime
ii. Unplanned downtime
iii. Idling and minor stoppages
iv. Slow-downs
v. Process nonconformities
vi. Scrap
14.Why is a conventional design process not sufficient?
Conventional design processes focus more on engineering capabilities and less on customer needs. When they do try to incorporate customer perspectives, these tend to be engineer-perceived or producer-perceived. Quality Function Deployment (QFD), however, focuses like a laser all product development activities on customer needs
15.How does QFD offer strategic advantage?
The expected and exciting requirements provide the best opportunity for competitive advantage - if you can find a way to make them visible and then deliver on them. However, in this fast changing world, hitting the right target of customer satisfaction is made more difficult by fragmenting customer segments, new technology, and competitive pressures. QFD makes invisible requirements and strategic advantages visible, allows you to prioritize and deliver on them in a focused product development process.
Regarding Taquchi,s Loss function
please follow the link for excellent intrduction given by Mr.Issa Bass SixSIgma FIrst Editor
Wednesday, March 01, 2006
UNIT-3 QUESTIONS AND ANSWERS
DEAR STUDENTS, IN ADDITION PLEASE REFER THE LECTURE NOTES FOR NUMERICAL PROBLEMS
1. Give the seven tools of quality?
i. Pareto Diagram
ii. Process Flow Diagram
iii. Cause-and-Effect Diagram
iv. Check Sheets
v. Histogram
vi. Control Charts
vii. Scatter Diagrams
2. Define Statistics?
Statistics is defined as the science that deals with the collection, tabulation, analysis, interpretation, and presentation of quantitative data.
3. What is a measure of central tendency?
A measure of central tendency of a distribution is a numerical value that describes the central position of the data or how the data tend to build up in the center. There are three measures in common in use in quality viz, the average, the median and the mode.
4. What is Measures of dispersion?
Measures of dispersion describe how the data are spread out or scattered on each side of the central value. The measures of dispersion used are range and standard deviation.
5. What is a normal curve?
The normal curve is a symmetrical, unimodal, bell-shaped distribution with the mean, median and mode having the same value.
6. What is the use of the control chart?
The control chart is used to keep a continuing record of a particular quality characteristic. It is a picture of process over time.
7. Give the objectives of the attribute charts?
i. Determine the average quality level.
ii. Bring to the attention of management any changes in the average.
iii. Improve the product quality.
iv. Evaluate the quality performance of operating and management personnel.
v. Determine acceptance criteria of a product before shipment to the customer.
8. Define Six Sigma Problem Solving Method?
Define - improvement opportunity with an emphasis on increasing customer satisfaction.
Measure - determine process capability (Cp/ Cpk) & dpmo (defects per million opportunities).
Analyze - identify the vital few process input variables that affect key product output variables (“Finding the knobs”).
Improve - Make changes to process settings, redesign processes, etc. to reduce the number of defects of key output variables.
Control - Implement process control plans, install real-time process monitoring tools, standardize processes to maintain levels.
9. What are the new seven management tools?
i. Affinity Diagram
ii. Interrelationship Digraph
iii. Tree Diagram
iv. Matrix Diagram
v. Prioritization Matrices
vi. Process Decision Program Chart
vii. Activity Network diagram
1. Give the seven tools of quality?
i. Pareto Diagram
ii. Process Flow Diagram
iii. Cause-and-Effect Diagram
iv. Check Sheets
v. Histogram
vi. Control Charts
vii. Scatter Diagrams
2. Define Statistics?
Statistics is defined as the science that deals with the collection, tabulation, analysis, interpretation, and presentation of quantitative data.
3. What is a measure of central tendency?
A measure of central tendency of a distribution is a numerical value that describes the central position of the data or how the data tend to build up in the center. There are three measures in common in use in quality viz, the average, the median and the mode.
4. What is Measures of dispersion?
Measures of dispersion describe how the data are spread out or scattered on each side of the central value. The measures of dispersion used are range and standard deviation.
5. What is a normal curve?
The normal curve is a symmetrical, unimodal, bell-shaped distribution with the mean, median and mode having the same value.
6. What is the use of the control chart?
The control chart is used to keep a continuing record of a particular quality characteristic. It is a picture of process over time.
7. Give the objectives of the attribute charts?
i. Determine the average quality level.
ii. Bring to the attention of management any changes in the average.
iii. Improve the product quality.
iv. Evaluate the quality performance of operating and management personnel.
v. Determine acceptance criteria of a product before shipment to the customer.
8. Define Six Sigma Problem Solving Method?
Define - improvement opportunity with an emphasis on increasing customer satisfaction.
Measure - determine process capability (Cp/ Cpk) & dpmo (defects per million opportunities).
Analyze - identify the vital few process input variables that affect key product output variables (“Finding the knobs”).
Improve - Make changes to process settings, redesign processes, etc. to reduce the number of defects of key output variables.
Control - Implement process control plans, install real-time process monitoring tools, standardize processes to maintain levels.
9. What are the new seven management tools?
i. Affinity Diagram
ii. Interrelationship Digraph
iii. Tree Diagram
iv. Matrix Diagram
v. Prioritization Matrices
vi. Process Decision Program Chart
vii. Activity Network diagram
QUESTIONS & ANSWERS-

1. What are the important factors that influenced purchases?
i. Performance
ii. Features
iii. Service
iv. Warranty
v. Price
vi. Reputation
2. Give the need for a feedback in an organization?
Discover customer dissatisfaction.
Discover relative priorities of quality.
Compare performance with the competition.
Identify customer’s needs.
Determine opportunities for improvement.
3. List the tools used for feedback?
Comment cards
Surveys
Focus groups
Toll-free telephone lines
Customer visits
Report cards
The internet
Employee feedback
American Customer Satisfaction Index
4. What are the activities to be done using customer complaints?
Investigate customer’s experience by actively soliciting feedback, both positive and negative, and then acting on it promptly.
Develop procedures for complaint resolution that include empowering front-line personnel.
Analyze complaints, but understand that complaints that do not always fit into neat categories.
Work to identify process and material variations and then eliminate the root cause. “More inspection” is not corrective action.
When a survey response is received, a senior manager should contact the customer and strive to resolve the concern.
Establish customer satisfaction measures and constantly monitor them.
Communicate complaint information, as well as the results of all investigations and solutions, to all people in the organization.
Provide a monthly complain report to the quality council for their evaluation and, if needed, the assignment of process improvement teams.
Identify customer’s expectations beforehand rather than afterward through complaint analysis.
5. What are the elements of customer service?
Organization
Customer care
Communication
Front-line people
Leadership
6. Define customer retention?
Customer retention represents the activities that produce the necessary customer satisfaction that creates customer loyalty, which actually improves the bottom line. It is the nexus between the customer satisfaction and the bottom line.
7. Define Employee Involvement?
Employee involvement is a means to better meet the organization’s goals for quality and productivity at all levels of an organization.
8. State Maslow’s Hierarchy of Needs?
Level 1 : Survival
Level 2 : Security
Level 3 : Social
Level 4 : Esteem
Level 5 : Self-actualization
9. State Frederick Herzberg’s Two-factor theory?
Herzberg found that people were motivated by recognition, responsibility, achievement and the work itself.
10. What does an employee want?
i. Interesting work
ii. Appreciation
iii. Involvement
iv. Job security
v. Good pay
vi. Promotion/growth
vii. Good working conditions
viii. Loyalty to employees
ix. Help with personal problems
x. Tactful discipline
11. What are the concepts to achieve a motivated work force?
a. Know thyself
b. Know your employees
c. Establish a positive attitude
d. Share the goals
e. Monitor progress
f. Develop interesting work
g. Communicate effectively
h. Celebrate success
12. Define Empowerment?
Empowerment means invest people with authority. Its purpose is to tap the enormous reservoir of creativity and potential contribution that lies within every worker at all levels.
Empowerment is an environment in which people have the ability, the confidence, and the commitment to take the responsibility and ownership to improve the process and to initiate the necessary steps to satisfy customer requirements within well-defined boundaries in order to achieve organizational values an goals.
13. What are the three conditions necessary to create the empowered environment?
i. Everyone must understand the need for change.
ii. The system needs to change for the new paradigm
iii. The organization must enable its employees.
14. What are the types of teams?
i. Process improvement team
ii. Cross-functional team
iii. Natural work teams
iv. Self-directed/self-managed work teams
15. What are the characteristics of successful teams?
a. Sponsor
b. Team charter
c. Team composition
d. Training
e. Ground rules
f. Clear objectives
g. Accountability
h. Well-defined decision procedures
i. Resources
j. Trust
k. Effective problem solving
l. Open communications
m. Appropriate leadership
n. Balanced participation
o. Cohesiveness
16. What are the decision-making methods?
a) Non decision
b) Unilateral decision
c) Handclasp decision
d) Minority-rule decision
e) Majority-rule decision
f) Consensus
17. What are the stages of team development?
i. Forming
ii. Storming
iii. Norming
iv. Performing
v. Adjourning
18. Give some common team problems?
I. Floundering
II. Overbearing participants
III. Dominating participants
IV. Reluctant participants
V. Unquestioned acceptance of opinions as facts
VI. Rush to accomplish
VII. Attribution
VIII. Discounts and “plops”
IX. Wanderlust : digression and tangents
X. Feuding team members
19. What are the common barriers to team progress?
i. Insufficient training
ii. Incompatible rewards and compensation
iii. First-line supervisor resistance
iv. Lack of planning
v. Lack of management support
vi. Access to information systems
vii. Lack of union support
20. Give the steps involved in training process?
1st. Make everyone aware of what the training is all about.
2nd. Get acceptance.
3rd. Adapt the program.
4th. Adapt to what has been agreed upon.
21. Define Recognition and Reward?
Recognition is a form of employee motivation in which the organization publicly acknowledges the positive contributions an individual or team has made to the success of the organization.
Reward is something tangible to promote desirable behavior. Recognition and reward go together to form a system for letting people know they are valuable members of the organization.
22. What are the types of appraisal formats?
i. Ranking
ii. Narrative
iii. Graphic
iv. Forced choice
23. What are the benefits of employee involvement?
Employee Involvement improves quality and increases productivity because
Employees make better decisions using their expert knowledge of the process.
Employees are more likely to implement and support decisions they had a part in making.
Employees are better able to spot and pinpoint areas for improvement.
Employees are better able to take immediate corrective action.
Employee involvement reduces labor/management hassle by more effective communications and cooperation.
Employee involvement increases morale by creating a feeling of belonging to the organization.
Employees are better able to accept change because they control the work environment.
Employees have an increased commitment to unit goals because they are involved.
24. What are the basic ways for a continuous process improvement?
Reduce resources
Reduce errors
Meet or exceed expectations of downstream customers
Make the process safer
Make the process more satisfying to the person doing it.
25. What are the three components of the Juran Trilogy?
i. Planning
ii. Control
iii. Improvement
26. What are the steps in the PDSA cycle?
The basic Plan-Do-Study-Act is an effective improvement technique.
1st. Plan carefully what is to be done
2nd. Carry out the plan
3rd. Study the results
4th. Act on the results by identifying what worked as planned and what didn’t.
27. What are the phases of a Continuous Process Improvement Cycle?
a) Identify the opportunity
b) Analyze the process
c) Develop the optimal solutions
d) Implement
e) Study the results
f) Standardize the solution
g) Plan for the future
28. Define 5S?
5S Philosophy focuses on effective work place organization and standardized work procedures. 5S simplifies your work environment, reduces waste and non-value activity while improving quality efficiency and safety.
Sort – (Seiri) the first S focuses on eliminating unnecessary items from the workplace.
Set In Order (Seiton) is the second of the 5Ss and focuses on efficient and effective storage methods.
Shine: (Seiso) Once you have eliminated the clutter and junk that has been clogging your work areas and identified and located the necessary items, the next step is to thoroughly clean the work area.
Standardize: (Seiketsu) Once the first three 5S’s have been implemented, you should concentrate on standardizing best practice in your work area.
Sustain: (Shitsuke) This is by far the most difficult S to implement and achieve.
Once fully implemented, the 5S process can increase morale, create positive impressions on customers, and increase efficiency and organization.
29. What is a Kaizen?
Kaizen is a Japanese word for the philosophy that defines management’s role in continuously encouraging and implementing small improvements involving everyone. It is the process of continuous improvement in small increments that make the process more efficient, effective, under control and adaptable.
30. What are the three key elements to a partnering relationship?
i. Long-term commitment
ii. Trust
iii. Shared vision
31. What are the three types of sourcing?
a) Sole sourcing
b) Multiple sourcing
c) Single sourcing
32. What are the ten conditions for the selection and evaluation of suppliers?
I. The supplier understands and appreciates the management philosophy of the organization.
II. The supplier has a stable management system.
III. The supplier maintains high technical standards and has the capability of dealing with future technological innovations.
IV. The supplier can supply precisely those raw materials and parts required by the purchaser, and those supplied meet the quality specifications.
V. The supplier has the capability to produce the amount of production needed or can attain that capability.
VI. There is no danger of the supplier breaching corporate secrets.
VII. The price is right and the delivery dates can be met. In addition, the supplier is easily accessible in terms of transportation and communication.
VIII. The supplier is sincere in implementing the contract provisions.
IX. The supplier has an effective quality system and improvement program such as ISO/QS 9000.
X. The supplier has a track record of customer satisfaction and organization credibility.
33. What are the four phases of inspection?
i. 100% inspection
ii. Sampling
iii. Audit
iv. Identity check
34. What are the objectives of Performance measures?
i. Establish baseline measures and reveal trends.
ii. Determine which processes need to be improved.
iii. Indicate process gains and losses.
iv. Compare goals with actual performance.
v. Provide information for individual and team evaluation.
vi. Provide information to make informed decisions.
vii. Determine the overall performance of the organization.
35. What are the characteristics used to measure the performance of a particular process?
i. Quantity
ii. Cost
iii. Time
iv. Accuracy
v. Function
vi. Service
vii. Aesthetics
36. Give the six basic techniques for presenting performance measures?
a) Time series graph
b) Control chart
c) Capability index
d) Taguchi’s Loss Function
e) Cost of poor quality
f) Malcolm Baldrige National Quality Award
Definition of Quality:
The dictionary has many definitions of “quality”. A short definition that has achieved acceptance is : “ Quality is Customer Satisfaction”. “Fitness for use” is an alternative short definition. Here, customer means anyone who is impacted by the product or process.
Quality is “ a predictable degree of uniformity and dependability, at low cost and suited to the market”.
Quality is a relative term, generally used with reference to the end-use of a product. Quality should be aimed at the needs of the consumer, present and future.
According to ISO 8402, quality is “ the totality of features and characteristics of a product or service that bear on its ability to satisfy stated or implied needs”.
Broadly quality is:
a) Fitness for use
b) Grade
c) Degree of preference
d) Degree of excellence
e) Conformity to requirements
Dimensions of Quality :
The following are the components reveal the dimensions of quality.
Manufacturing Industries Service Industries
Product Features Accuracy
Performance Timeliness
Reliability Completeness
Durability Friendliness and courtesy
Ease of use Anticipating customer needs
Serviceability Knowledge of server
Esthetics Esthetics
Availability Reputation
Reputation
Quality Planning :
Quality planning is the pre determined activities in order to achieve conformation to the requirements. Many organizations are finding that strategic quality plans and business plans are inseparable. The quality planning procedure given by Joseph.A.Juran has the following steps:
· Identify the customers
· Determine their needs
· Translate those needs into our language.
· Develop a product that can respond to those needs
· Optimize the product features to meet our and customer needs
Quality Costs :
All organizations make use of the concept of identifying the costs needed to carry out the various functions – product development, marketing, personnel, production etc.,
Until the 1950’s this cost concept had not been extended to quality function, except for the departmental activities of inspection and testing.
During the 1950’s the concept of “Quality Cost” emerged. Different people assigned different meanings to the term. Some people equated quality cost with the cost of attaining quality; some people equated the term with the extra incurred due to poor quality. But, the widely accepted thing is “Quality cost is the extra cost incurred due to poor or bad quality of the product or service”.
Categories of Quality Cost :
Many companies summarize quality costs into four broad categories. They are,
a) Internal failure costs - The cost associated with defects that are found prior
to transfer of the product to the customer.
b) External failure costs - The cost associated with defects that are found after
product is shipped to the customer.
c) Appraisal costs - The cost incurred in determining the degree of
conformance to quality requirement.
d) Prevention costs - The cost incurred in keeping failure and appraisal
costs to a minimum.
Some times we can also include the hidden costs ie., implicit costs.
Traditional Quality cost model

Emerging Quality Cost Model
... yes, higher quality quality doesn't mean higher costs

The companies estimate quality costs for the following reasons :
a) To quantifying the size of the quality problem in the language of money improves communication between middle managers and upper managers.
b) To identify major opportunities for cost reduction.
c) To identify the opportunities for reducing customer dissatisfaction and associated threats to product salability.
Analysis Techniques for Quality Costs :
Refer the recommended text book.
Basic Concepts of Total Quality Management :

Definition of TQM:
Total Quality Management is a management approach that tries to achieve and sustain long term organizational success by encouraging employee feedback and participation, satisfying customer needs and expectations, respecting societal values and beliefs, and obeying governmental statutes and regulations.
Five Pillars of TQM are,
· Product
· Process
· System
· People
· Leadership
Total Quality Management is an effective system for integrating the quality development, quality maintenance and quality improvement efforts of various groups in an organization continuously, so as to enable marketing, engineering, production and service at the most economic levels which allow for full customer satisfaction.
The TQM is applied to many stages of Industrial Cycle which are listed below :
1. Marketing
2. Engineering
3. Purchasing
4. Manufacturing
5. Mechanical
6. Shipping
7. Installation and product service.
<
strong>Fundamental factors affecting Quality : ( 9 M’s)
1. Market
2. Money
3. Management
4. Men
5. Motivation
6. Materials
7. Machines and Mechanization
8. Modern Information Methods
9. Mounting Product Requirements
Benefits of TQM :
Customer satisfaction oriented benefits :
1. Improvement in product quality
2. Improvement in product design
3. Improvement in production flow
4. Improvement in employee morale and quality consciousness
5. Improvement in product service
6. Improvement in market place acceptance
Economic improvement oriented benefits :
1. Reduction in operating costs
2. Reduction in operating losses
3. Reduction in field service costs
4. Reduction in liability exposure
Historical Review :
The history of quality control is undoubtedly as old as industry itself.
In 1924, W.A. Shewhart of Bell Telephone Laboratories developed a statistical chart of the control of product variables. This chart is considered to be the beginning of statistical quality control. Later in the same decade, H.F.Dodge and H.G.Romig, both of Bell Telephone Laboratories, developed the area of acceptance sampling as a substitute of 100% inspection.
In 1946, the American society for Quality Control was formed. Recently the name was changed into Americn Society for Quality (ASQ).
In 1950’s W.Edwards Deming emphasized about the management’s responsibility to achieve quality.
In 1960’s the first quality control circles were formed for the purpose of quality improvement.
In the late 1980’s the automotive industry began to emphasize statistical process control.
After 1990’s the ISO became the model for a quality management system world wide.
Principles of TQM :
Visionary leadership
Customer-driven excellence
Organizational and personal learning
Valuing employees and partners
Agility
Focus on the future
Managing for innovation
Management by fact
Public responsibility
Focus of results and creating values
Systems perspective
Leadership :

Leadership plays a central part in understanding group behavior, for it is the leader who usually provides the direction toward goal attainment. Therefore, a more accurate predictive capability should be valuable in improving group performance.
We can define leadership as “the ability to influence a group toward the achievement of
goals.”
· The source of this influence may be formal. A person may assume a leadership role simply because of his/her position.
· Not all leaders are managers, nor, for that matter, are all managers leaders.
· Non-sanctioned leadership—the ability to influence that arises outside the formal structure of the organization—is often as important as or more important than formal influence.
· Leaders can emerge from within a group as well as by formal appointment to lead a group.
Organizations need strong leadership and strong management for optimum effectiveness.
Leaders must challenge the status quo, create visions of the future, and inspire
organizational members.
Six traits on which leaders tend to differ from non leaders are:
a. Ambition and energy
b. Desire to lead
c. Honesty and integrity
d. Self-confidence
e. Intelligence
f. Job-relevant knowledge.
Characteristics of Quality Leaders:
They continuously evaluate the changing customer needs.
They empower, rather than control subordinates.
They emphasize improvement rather than maintenance
They emphasize prevention.
They encourage collaboration rather than competition.
They train and coach rather than direct and supervise.
They learn from the problems.
They continuously improve communication.
They continuously committed to quality.
They choose suppliers in the basis of quality not price.
They establish organizational system to support quality effort.
They encourage and recognize team effort.
Quality Council :
In order to build quality in the culture, a quality council is established to provide overall direction. It is the driver for the TQM engine.
In a typical organization the quality council is composed of the chief executive officer (CEO); the senior managers of the functional areas, such as design, marketing, finance, production, and quality; and a Coordinator or consultant.
Duties of the quality council:
a) To develop the vision, mission and quality statement of the organization, with the input from all the personnel.
b) To develop strategic long-term plan with goals and annual quality improvement program with objectives.
c) Create a total education and training plan.
d) Determine and continuously monitor the cost of poor quality.
e) Determine the performance measures of the organization and monitor.
f) Continuously determine those projects that improves and affect external and internal customer satisfaction.
g) Establish multifunctional project and work group teams and monitor their progress.
h) Establish and revise the recognition and reward system to account for the new way of doing business.
The typical quality council meeting agenda of a well established TQM organization :
a) Progress reports on teams
b) Customer satisfaction report
c) Progress on meeting goals
d) New project teams
e) Recognition dinner
f) Benchmarking report
Quality Statements :

Core values and concepts provide the unity of purpose. In addition to that, the quality statements include the vision statement, mission statement and quality policy statement. They are the part of the strategic planning process.
Vision Statement:
It is a short declaration of what an organization aspires to be tomorrow. It is the ideal state that might never reached but which you continuously strive to achieve.
Example :
We will be the preferred provider of safe, reliable, and cost-effective products and services that satisfy the electric-related needs of all customer segments.
FLORIDA POWER & LIGHT COMPANY
Mission Statement :

The mission statements answers the following questions :
Who we are ? Who are the customers ? What we do ? and How we do it ?
It is the usually a one paragraph statement which describes the function of the organization. It provides a clear statement of purpose for employees, customers and suppliers.
Example :
To meet customers’ transportation and distribution needs by being the best at moving their goods on time, safely and damage free.
CANADIAN NATIONAL RAILWAYS
Strategic Planning :

There are seven basic steps to strategic quality planning.
a) Customer needs
b) Customer positioning
c) Predict the future
d) Gap analysis
e) Closing the gap
f) Alignment
g) Implementation
Strategic planning can be performed by any organization . It can be highly effective, allowing organizations to do the right thing at the right time, every time.
Deming Philosophy :
W. Edwards Deming, an American quality expert, become a Parama-Guru in Japan because he preached the philosophical basis of quality and productivity, which were accepted, absorbed and implemented with sustained positive results by the Japanese.
The Highest Award inn the Japanese Industrial Circles is the Deming prize for quality.

Dr. Deming introduced the Plan –Do-Study-Act cycle to the Japanese decades ago.
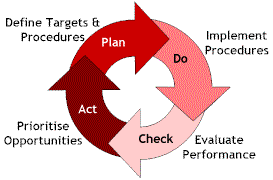
A Company plans a change, does it, checks the results and depending upon the results, acts either to standardize the change or to begin the cycle of improvement again with new information.
Continuous or never ending improvement requires such a circular approach.
Deming’s Philosophy is given in his 14 points of quality management. Most of these points were given in a seminar for 21 presidents of leading Japanese industry in 1950. The rest were developed and the original ones modified over a period of three decades.
1.Create and publish the aims and purposes of the organization.
2.Learn the new philosophy.
3.Understand the purpose of inspection.
4.Stop awarding business based on price alone.
5.Improve constantly and forever the system.
6.Institute training.
7.Teach and institute leadership.
8.Drive out fear, create trust and create a climate for innovation.
9.Optimize the efforts of teams, groups and staff areas.
10.Strive to eliminate intradepartmental conflicts
11Eliminate exhortations for the work force.
a) Eliminate numerical quotas for the work force.
b) Eliminate Management by Objective.
12.Remove barriers that rob people of pride of workmanship.
13.Encourage education and self-improvement of everyone.
14.Take action to accomplish the transformation.
In addition he also pointed out the 7 deadly diseases that affecting the above transformation
The Seven Deadly Diseases
1. Lack of constancy of purpose.
2. Emphasis on short-term profits.
3. Evaluation by performance, merit rating, or annual review of performance.
4. Mobility of management.
5. Running a company on visible figures alone.
6. Excessive medical costs.
7. Excessive costs of warranty, fueled by lawyers that work on contingency fee.
A Lesser Category of Obstacles
1. Neglect of long-range planning.
2. Relying on technology to solve problems.
3. Seeking examples to follow rather than developing solutions.
4. Excuses such as "Our problems are different".
5. Others.
Barriers to TQM Implementation :

Lack of management commitment
Inability to change organizational culture
Improper planning
Lack of continuous training and education
Incompatible organizational structure and isolated individuals and department
Ineffective measurement techniques and lack of access to data and results
Paying inadequate attention to internal and external customers
Inadequate use of empowerment and team work
Failure to continually improve
--------------------------------------------------------------------------------
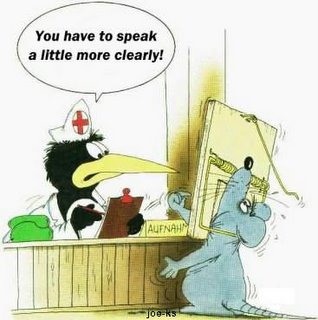
Dear students given below is the typical questions and answers for Unit-1, here I've answered all the questions without considering it as a Part-A or Part-B following the text book(since the Anna University Evaluation key will be usually based on the prescribed text book).
However student can write a gist of answer for Part-A, and can elaboratre in the case of Part-B questions.
If you've any doubt, or any suggestions please commment this post.
1. Define Total Quality Management?
TQM is an enhancement to the traditional way of doing business. It is the art of managing the whole to achieve excellence. It is defined both a philosophy and a set of guiding principles that represent the foundation of a continuously improving organization. It is the application of quantitative methods and human resources to improve all the processes within an organization and exceed customer needs now and in the future. It integrates fundamental management techniques, existing improvement efforts, and technical tools under a disciplined approach.you can also write Juran or Deming's definition given in the class lectures
2. Define Quality?
conformance to specifications
fitness for purpose
customer satisfaction
Quality = Performance x Expectations
Also you can write ISO definition quality.
(Oooh..., after all any definition to quality is only subjective...)
3. What are the Dimensions of Quality?
- Performance
- Features
- Conformance
- Reliability
- Durability
- Service
- Response
- Aesthetics
- Reputation
§ A committed and involved management to provide long-term top-to-bottom organizational support.
§ An unwavering focus on the customer, both internally and externally.
§ Effective involvement and utilization of the entire work force.
§ Continuous improvement of the business and production process.
§ Treating suppliers as partners.
§ Establish performance measures for the processes.
5. State Deming Philosophy?
Create and publish the aims and purposes of the organization.
Learn the new philosophy.- Understand the purpose of inspection.
- Stop awarding business based on price alone.
- Improve constantly and forever the system.
- Institute training.
- Teach and institute leadership.
- Drive out fear, Create trust and Create a climate for innovation.
- Optimize the efforts of teams, groups and staff areas.
- Eliminate exhortations for the work force.
- Eliminate numerical quotes for the work force.
- Eliminate management by objective.
- Remove barriers that rob people of pride of workmanship.
Encourage education and self-improvement for everyone. - Take action for accomplish the transformation.
6. Give the Principles of TQM?
1. Constancy of purpose: short range and long range objectives aligned
2. Identify the customer(s); Customer orientation
3. Identification of internal and external customers
4. Continuous improvement
5. Workflow as customer transactions
6. Empower front-line worker as leader
7. Quality is everybody’s business
8. For a service industry, some elements of quality are:
- empathy
- trust; i.e. expertise, integrity, courtesy
- responsiveness
- tangible product attractiveness (curb appeal)
- reliability, on time, no interruptions
Brief explanation required in the case of part-B answer.
7. Give the Obstacles associated with TQM Implementation?
- Lack of management commitment
- Inability to change organizational culture
- Improper planning
- Lack of continuous training and education
- Incompatible organizational structure and isolated individuals and departments
- Ineffective measurement techniques and lack of access to data and results.
- Paying inadequate attention to internal and external customers.
- Inadequate use of empowerment and teamwork.
i. Trend Analysis
ii. Pareto Analysis
9. Define Quality Costs?
Quality Costs are defined as those costs associated with the non-achievement of product or service quality as defined by the requirements established by the organization and its contracts with customers and society.
or stated simply cost of poor quality products.
10. Give the primary categories of Quality cost?
PAF costs
i. Preventive cost category
ii. Appraisal cost category
iii. Internal failure cost category
iv. External failure cost category
11. Give the sub-elements of Preventive cost category?
i. Marketing/Customer/User
ii. Product/Service/Design development
iii. Purchasing
iv. Operations/
v. Quality Administration
vi. Other Prevention Costs
12. Give the sub-elements of Appraisal cost category?
i. Purchasing appraisal cost
ii. Operations appraisal cost
iii. External appraisal cost
iv. Review of test and application data
v. Miscellaneous quality evaluations
13. Give the sub-elements of Internal failure cost category?
i. Product or Service Design costs (Internal)
ii. Purchasing failure costs
iii. Operations failure costs
14. Give the sub-elements of External failure cost category?
i. Complaint investigations of customer or user service
ii. Returned goods
iii. Retrofit and recall costs
iv. Warranty claims
v. Liability costs
vi. Penalties
vii. Customer or user goodwill
viii. Lost sales
ix. Other external failure costs
15. Give the typical cost bases?
i. Labor
ii. Production
iii. Unit
iv. Sales
16. How will you determine the optimum cost?
a. Make comparison with other organizations
b. Optimize the individual categories
c. Analyze the relationships among the cost categories
17. State the Quality Improvement Strategy?
- Ö Reduce failure costs by problem solving
- Ö Invest in the “right” prevention activities
- Ö Reduce appraisal costs where appropriate and in a statistically sound manner
- Ö Continuously evaluate and redirect the prevention effort to gain further quality improvement.
18. Define Quality Planning?
A quality plan sets out the desired product qualities and how these are assessed and define the most significant quality attributes. It should define the quality assessment process. It should set out which organizational standards should be applied and, if necessary, define new standards.
19. Give the Objectives of TQM?
a. To develop a conceptual understanding of the basic principles and methods associated with TQM;
b. To develop an understanding of how these principles and methods have been put into effect in a variety of organizations;
c. To develop an understanding of the relationship between TQM principles and the theories and models studied in traditional management;
d. To do the right things, right the first time, every time.
20. Give the Quality Hierarchy?
1. Inspection (QI)
2. Quality Control (QC)
3. Quality Assurance (QA)
4. Total Quality Management (TQM)
Inspect products.
Detection
Finding &
Fixing Mistakes.
21. What is needed for a leader to be effective?
To be effective, a leader needs to know and understand the following:
è People, paradoxically, need security and independence at the same time.
è People are sensitive to external rewards and punishments and yet are also strongly self-motivated.
è People like to hear a kind word of praise.
è People can process only a few facts at a time; thus, a leader needs to keep things simple.
è People trust their gut reaction more than statistical data.
è People distrust a leader’s rhetoric if the words are inconsistent with the leader’s actions.
22. What is the important role of senior management?
§ Listening to internal and external customers and suppliers through visits, focus groups and surveys.
§ Communication.
§ To drive fear out of the organization, break down barriers, remove system roadblocks, anticipate and minimize resistance to change and in general, change the culture.
23. What are the general duties of a quality council?
i. Develop, with input from all personnel, the core values, vision statement, mission statement, and quality policy statement.
ii. Develop the strategic long-term plan with goals and the annual quality improvement program with objectives.
iii. Create the total education and training plan.
iv. Determine and continually monitor the cost of poor quality.
v. Determine the performance measures for the organization, approve those for the functional areas, and monitor them.
vi. Continually, determine those projects that improve the processes, particularly those that affect external and internal customer satisfaction.
vii. Establish multifunctional project and departmental or work group teams and monitor their progress.
viii. Establish or revise the recognition and reward system to account for the new way of doing business.
24. What does a typical meeting agenda contain after establishing the TQM?
Progress report on teams
Customer satisfaction report
Progress on meeting goals
New project teams
Recognition dinner
Benchmarking report
25. What are the various quality statements?
Vision Statement
Mission Statement
Quality Policy Statement
26. Give the basic steps to strategic quality planning?
i.Customer needs
ii. Customer positioning
iii.Predict the future
iv.Gap analysis
v.Closing the gap
vi.Alignment
vii.Implementation
27. What is a quality policy
The Quality Policy is a guide for everyone in the organization as to how they should provide products and service to the customers. The common characteristics are
Quality is first among equals.
Meet the needs of the internal and external customers.
Equal or exceed the competition.
Continually improve the quality.
Include business and production practices.
Utilize the entire work force.
28. What is a mission statement?
The mission statement answers the following questions: who we are, who are the customers, what we do, and how we do it.
29. What is a vision statement?
The vision statement is a declaration of what an organization should look like five to ten years in a future.
In developing this list of Frequently Asked Questions (FAQ's), input has been obtained from experts and users of the ISO 9000 standards from around the world. The list will be reviewed and updated on a regular basis to maintain its accuracy, and to include new questions where appropriate. It is intended that this list will also provide a good source of information for new users of the standards.
What is ISO?
The International Organization for Standardization (ISO) was established in 1947 and is (currently) an association of approximately 149 National Standards Bodies, which each represent their own country. ISO employs a system of Technical Committees, Sub-committees and Working Groups to develop International Standards. Besides the National Standards Bodies, ISO permits other international organizations that develop standards to participate in its work, by accepting them as Liaison members. ISO works in accordance with an agreed set of rules of procedure, the ISO/IEC Directives, which also include requirements on the presentation of standards. For further details please refer to ISO's own web site at http://www.iso.org
Who are the National Standards Bodies, and who represents my country at ISO?
Please use the link on ISO's web site that gives details, including contact information, of the National Standards Bodies: http://www.iso.org/iso/en/aboutiso/isomembers/index.html[FAQ 002, April 2004]
What are the ISO 9000 standards ?
The ISO 9000 standards are a collection of formal International Standards, Technical Specifications, Technical Reports, Handbooks and web based documents on Quality Management and Quality Assurance. There are approximately 25 documents in the collection altogether, with new or revised documents being developed on an ongoing basis.
(It should be noted that many of the International Standards are numbered in the ISO 10000 range.)
Who is responsible for developing the ISO 9000 standards?
ISO Technical Committee (TC) number 176 (ISO/TC 176), and its Sub-committees, are responsible for the development of the standards. The work is conducted on the basis of "consensus" among quality and industry experts nominated by the National Standards Bodies, representing a wide range of interested parties. Where can copies of the standards be obtained?
Copies of the standards may be purchased from your National Standards Body, or from ISO itself (sales@iso.org). Many National Standards Bodies have them available in local-language versions. [FAQ 005, April 2004]
Where can information be obtained on the ISO 9000 standards?
There are a number of sources of information on the ISO 9000 quality management system standards, including this web site and the ISO/TC 176 Web site, which carry information on the standards. Your National Standards Body should be able to provide copies of the standards, and registrars/certification bodies will be able to provide guidance on registration arrangements.[FAQ 006, April 2004]
Where should an organization go if it needs clarification or interpretation of the standards?
The starting point for an interpretation should be with your National Standards Body. ISO Central Secretariat and ISO/TC 176 cannot accept direct requests from individuals for interpretations of the ISO 9000 standards. Instead, ISO/TC 176 has established a Working Group for interpretation, with a formal procedure to provide answers to the questions that are forwarded by the National Standards Bodies. Details of agreed interpretations are now being published on the ISO/TC 176 web site at http://www.tc176.org. [FAQ 007, April 2004]
What happened to the 1994 editions of ISO 9001, ISO 9002 and ISO 9003?
Following extensive consultation with users and National Standards Bodies, it was agreed that the 1994 editions of ISO 9001, ISO 9002 and ISO 9003 should be consolidated into a single revised document, which is now represented by ISO 9001:2000.[FAQ 008, April 2004]
What are the main benefits to be derived from implementing an ISO 9000 quality management
system?
The ISO 9000 standards give organizations an opportunity to increase value to their activities and to improve their performance continually, by focusing on their major processes. The standards place great emphasis on making quality management systems closer to the processes of organizations and on continual improvement. As a result, they direct users to the achievement of business results, including the satisfaction of customers and other interested parties.
The management of an organization should be able to view the adoption of the quality management system standards as a profitable business investment, not just as a required certification issue.
Among the perceived benefits of using the standards are:
The connection of quality management systems to organizational processes
The encouragement of a natural progression towards improved organizational performance, via:
the use of the Quality Management Principles
the adoption of a "process approach"
emphasis of the role of top management
requirements for the establishment of measurable objectives at relevant functions and levels
being orientated toward "continual improvement" and "customer satisfaction", including the monitoring of information on "customer satisfaction" as a measure of system performance
measurement of the quality management system, processes, and product
consideration of statutory and regulatory requirements
attention to resource availability
The concept of a "consistent pair" of standards; with ISO 9001 establishing initial requirements and ISO 9004 for going beyond the requirements to further improve the performance of the organization
Consideration of the needs of all interested parties.
The concept of organizational self-assessment as a driver for improvement (see ISO 9004:2000) .What benefits are there to an organization implementing ISO 9004?
If a quality management system is appropriately implemented, utilizing the eight Quality Management Principles, and in accordance with ISO 9004, all of an organization's interested parties should benefit. For example:
Customers and users will benefit by receiving the products (see ISO 9000:2000) that are:
Conforming to the requirements
Dependable and reliable
Available when needed
Maintainable
People in the organization will benefit by:
Better working conditions
Increased job satisfaction
Improved health and safety
Improved morale
Improved stability of employment
Owners and investors will benefit by:
Increased return on investment
Improved operational results
Increased market share
Increased profits
Suppliers and partners will benefit by:
Stability
Growth
Partnership and mutual understanding
Society will benefit by:
Fulfilment of legal and regulatory requirements
Improved health and safety
Reduced environmental impact
Increased security
Are the standards compatible with national quality award criteria?
The standards are based on 8 Quality Management Principles, which are aligned with the philosophy and objectives of most quality award programs. These principles are:
Customer focus
Leadership
Involvement of people
Process approach
System approach to management
Continual improvement
Factual approach to decision making
Mutually beneficial supplier relationships.
ISO 9004:2000 recommends that organizations perform self-assessments as part of their management of systems and processes, and includes an annex giving guidance on this approach. This is similar to many quality awards programmes.
Do the standards address financial issues?
Financial issues are not directly addressed in ISO 9001:2000, but may be inferred though the requirements for the provision of resources. ISO 9004:2000 gives guidance that emphasizes the financial resources needed for the implementation and improvement of a quality management system. ISO/TR 10014:1998 "Guidelines for managing the economics of quality" also gives further guidance.
How will implementation of the standards help an organization to improve its efficiency?
ISO 9001:2000 aims at guaranteeing the effectiveness (but not necessary the efficiency) of an organization. For improved organizational efficiency, however, the best results can be obtained by using the guidance given in ISO 9004:2000 in addition to ISO 9001:2000. Additionally, the guiding Quality Management Principles are intended to assist an organization in continual improvement, which should lead to efficiency throughout the organization.
Why is the requirement for monitoring "customer satisfaction" included in ISO 9001?
"Customer satisfaction" is recognized as one of the driving criteria for any organization. In order to evaluate if a product meets customer needs and expectations, it is necessary to monitor the extent of customer satisfaction. Improvements can be made by taking action to address any identified issues and concerns.
Can the standards improve "customer satisfaction"?
The quality management system details that are described in the standards are based on Quality Management Principles that include the "process approach" and "customer focus". The adoption of these principles should provide customers with a higher level of confidence that products will meet their needs and increase their satisfaction.
What is the "process approach"?
The "process approach" is a way of obtaining a desired result, by managing activities and related resources as a process. The "process approach" is a key element of the ISO 9000 standards. For further guidance, please refer to the ISO 9000 Introduction and Support Package module: Guidance on the Concept and Use of the Process Approach for management systems.
Can the "process approach" be applied to other management systems?
Yes. The "process approach" is a generic management principle, which can enhance an organization’s effectiveness and efficiency in achieving defined objectives.How can the PDCA cycle be used in the "process approach"?
The PDCA cycle is an established, logical, method that can be used to improve a process.
This requires:
(P) planning (what to do and how to do it),
(D) executing the plan (do what was planned),
(C) checking the results (did things happened according to plan) and
(A) act to improve the process (how to improve next time).
The PDCA cycle can be applied within an individual process, or across a group of processes.
Can any organization apply the "process approach"?
Yes. Many organizations already apply a "process approach" without recognizing it. They could achieve additional benefits by understanding and controlling it.Why should an organization apply the "process approach"?
By applying the "process approach" an organization should be able to obtain the following types of benefits:
The integration and alignment of its processes to enable the achievement of its planned results.
An ability to focus effort on process effectiveness and efficiency.
An increase in the confidence of customers and other interested parties as to the consistent performance of the organization.
Transparency of operations within the organization.
Lower costs and shorter cycle times through effective and efficient use of resources.
Improved, consistent and predictable results.
The identification of opportunities for focused and prioritized improvement initiatives.
The encouragement and involvement of people, and the clarification of their responsibilities.
The elimination of barriers between different functional units and the unification of their focus to the objectives of the organization.
Improved management of process interfaces.
What is meant by the "sequence" of processes and their "interactions"?
The "sequence" of processes shows how the processes follow, or link, to each other to result in a final output.
For example, one process may become the output of the next process or processes.
The "interactions" show how each process affects or influences one or more of the other processes. For example, the monitoring or controlling of a process may be established in a separate process.
How can the processes in an organization be determined?
Identify the organization's intended outputs, and the processes needed for achieving them. These will need to include processes for Management, Resources, Realization and Measurement and Improvement.
Identify all process inputs and outputs, along with the suppliers and customers, who may be internal or external.
Identify the sequence and interactions of the processes.
Should an organization define and document all its processes?
The main purpose of documentation is to enable the consistent and stable operation of an organization's processes.
Although statutory, standards' or customer requirements may require certain documentation, there is no defined “catalogue”, or list of processes that has to be documented in ISO 9001, apart from the 6 indicated ones.
The organization should determine which processes are to be documented on the basis of:
The size of the organization and type of its activities,
The complexity of its processes and their interactions,
The criticality of the processes and
Availability of competent personnel.
A number of different methods can be used to document processes, such as graphical representations, written instructions, checklists, flow charts, visual media, or electronic methods.
How much detail is required in process documentation?
The extent of detail is likely to depend upon factors such as:
he size of an organisation and its types of activities,
the complexity of its processes and their interactions, and
the competence (level of education, training, skills and experience) of its personnel.
Is there a standard way of describing a process?
No, there is no standard way to describe a process. It depends on the culture, management style, staff literacy, personal attributes and their interactions.
A process may be described using a flow chart, block diagram, responsibility matrix, written procedures or pictures.
Process flowcharts or block diagrams can show how policies, objectives, influential factors, job functions, activities, material, equipment, resources, information, people and decision making interact and/or interrelate in a logical order.
What should an organization do to adopt the "process approach"?
To adopt the "process approach" an organization should apply the following steps:
Identify the processes of the organization,
Plan the processes,
Implement and measure the processes,
Analyse the processes,
Improve the processes.
What is a "process owner"?
A person who is given the responsibility and authority for managing a particular process is sometimes referred to as the "process owner".
It may be useful for an organization's Management to appoint individual "process owners" and to define their roles and responsibilities; these should include the responsibility for ensuring the implementation, maintenance and improvement of their specific process and its interactions.
It should be noted, however, that ISO 9001:2000 does not specifically require the appointment of "process owners".
How can a process be measured?
There are various methods of measuring process controls and process performance, ranging from simple monitoring systems up to sophisticated statistically based systems (e.g. Statistical process control, or SPC, systems). The selection and use of any particular method will be dependent on the nature and complexity of an organization's processes and products. The effectiveness of an individual process may be measured by the conformity of its output or product to customer requirements. Its efficiency may be measured from its use of resources. In all cases the measurement of the process determines if its (measurable) objectives have been achieved. Sometimes it only requires monitoring to confirm process operations.
Typical factors that are useful to consider when identifying measures of process control and process performance include:
Conformity with requirements,
Customer satisfaction,
Supplier performance,
On time delivery,
Lead times,
Failure rates,
Waste,
Process costs.
Incident frequency
What is the difference between a "process" and a "procedure"?
A "process" may be explained as a set of interacting or interrelated activities, which are employed to add value. A "procedure" is a method of describing the way in which all or part of that process is to be performed.
ISO 9000:2000 defines a procedure as a "specified way to carry out an activity or a process", which does not necessarily have to be documented.
An organization has a well-established set of procedures. Can these procedures be used to help describe its processes?
Yes, if the procedures describe inputs and outputs, appropriate responsibilities, controls and resources needed to satisfy customer requirements.
What is meant by "continual improvement"?
ISO 9001 requires an organization to focus on continually increasing the effectiveness of its quality management system, to fulfil its policies and objectives. One way of doing this is for the organization to improve its processes. The organization may also wish to consider improving the efficiency of its processes, for which ISO 9004:2000 provides guidance. Continual improvement (where "continual" highlights that an improvement process requires progressive consolidation steps) responds to the growing needs and expectations of customers and ensures a dynamic evolution of the quality management system.
What documentation is required by ISO 9001?
ISO 9001:2000 refers specifically to only 6 documented procedures; however, other documentation (including more documented procedures not specifically mentioned in ISO 9001:2000) may be required by an organization, in order to manage the processes that are necessary for the effective operation of the quality management system. This will vary depending on the size of the organization, the kind of activities in which it is involved and their complexity. For further guidance, please also refer to the ISO 9000 Introduction and Support Package module Guidance on the Documentation Requirements of ISO 9001:2000
Which standard are organizations registered/certified to?
Organizations have their quality management system registered/certified to ISO 9001:2000. The scope of registration/ certification will need to reflect precisely and clearly the activities covered by the organization's quality management system; any exclusion to non-applicable requirements of the standard (permitted through ISO 9001 clause 1.2 "Application") will need to be documented and justified in the quality manual (see also the ISO/TC 176/SC2 ISO 9000 Introduction and Support Package module Guidance on ISO 9001:2000 clause 1.2 'Application).
What does an organization need to do to comply with ISO 9001?
When initially starting to use ISO 9001, an organization should familiarize its personnel with the Quality Management Principles, analyze the standards (especially ISO 9004), and consider how their guidance and requirements may affect your activities and related processes. If it then wishes to proceed to registration/certification, it should perform a gap analysis against the requirements of ISO 9001 to determine where its current quality management system does not address the applicable ISO 9001:2000 requirements, before developing and implementing additional processes to ensure that compliance will be achieved. Can an organization be certified/registered to ISO 9004:2000?
ISO 9004:2000 is a guidance standard, which is not intended to be used for third party registration/certification purposes. A key element of ISO 9004 is the ability to perform self-assessments. Third party quality management system certifications/ registrations are performed to ISO 9001:2000.
What is the purpose of having ISO 9001 and ISO 9004 as a "consistent pair" of standards?
The idea of a "consistent pair" of standards is central to ISO 9001:2000 and ISO 9004:2000. The aligned structures of ISO 9001 and ISO 9004 have been designed to encourage organizations to look at their activities from a process standpoint, and also to look beyond the achievement of registration/certification to ISO 9001, to the implementation of a quality management system that will be truly beneficial in improving operational performance.
How does ISO 9001:2000 relate to the needs of specific business sectors?
The text of ISO 9001:2000 is applicable to organizations that provide different types of product and to organizations of different sizes. Due to this generic nature, some industrial or commercial sectors find that they need to identify additional requirements to attend to their specific requirements, so develop their own standards or related documents.
To assure consistency between the ISO 9001 requirements and sector requirements, ISO's rules of procedure require that ISO/TC 176 be invited to review sectoral documents while they are being developed by ISO. A successful example of such a document is ISO Technical Specification ISO/TS 16949, which was developed in conjunction with representatives from the automotive industries.
Is an organization's ISO 9001 certificate applicable to all of its produ
cts ?
When an organization seeks to have its quality management system registered/certified to ISO 9001:2000, it is required to agree a "scope of certification" with its registrar/certification body. This will define the products to which the organization's quality management system is applicable, and against which it will be assessed. An organization is not obliged to include within its "scope of certification" all the products that it provides (note that the ISO 9000:2000 definition of "Product" includes "services"), but may be selective about those that are included. All applicable requirements of ISO 9001:2000 will need to be addressed by the organization's quality management system that covers those products that are included in the "scope of certification".
Customers should ensure that a potential supplier's "scope of certification" covers the products that they wish to order. Caveat Emptor!
What can an organization do if it is not able to comply with all of the requirements of ISO 9001?
ISO 9001 allows for the exclusion of some of its requirements (via clause 1.2 'Application'), but only if it can be shown that these requirements are not applicable to the organization.
Exclusions are limited to the requirements given in Section 7 ("Product Realization"), where individual requirements may only be excluded if it can be shown that they do not affect the organization's ability to provide product that meets customer and applicable statutory or regulatory requirements. Justification for such exclusions is also required to be detailed within the organization's quality manual.
For example, if design activities are not required by an organization to demonstrate its capability to meet customer and applicable statutory /regulatory requirements, or if its product is provided on the basis of established design, then it may be able to exclude some of the "design" requirements but still be able to be registered/certified to ISO 9001:2000.
For further guidance, see the ISO 9000 Introduction and Support Package module: Guidance on ISO 9001:2000 clause 1.2 'Application'.
How will a small organization be able to adapt the requirements of ISO 9001? What flexibility will be allowed?
The requirements of ISO 9001 are applicable to small, medium, and large organizations alike. ISO 9001:2000 provides some flexibility, through clause 1.2 “Application”, on the exclusion of certain requirements for specific processes that may not be performed by the organization.
If, for example, the nature of your products does not require you to perform design activities, or if your product is provided on the basis of established design, you could discuss and justify the exclusion of these requirements with your certification/registration body (see also the ISO 9000 Introduction and Support Package module Guidance on ISO 9001:2000 clause 1.2 'Application'). However, individual organizations will still need to be able demonstrate their capability to meet customer and applicable statutory or regulatory requirements for their products, and will need to consider this when determining the complexity of their quality management systems.
Further guidance for small businesses may be found in ISO Handbook: ISO 9001:2000 for Small Businesses - What to do, Advice from ISO/TC 176.
What is the relationship between ISO 9001 and ISO 14001?
ISO 9001 has been developed to be "compatible" with ISO 14001 Environmental management systems – Requirements with guidance for use, particularly with regard to terminology and content.
There is close collaboration between the technical experts of ISO/TC 176 and ISO/TC 207 (the Technical Committee responsible for the ISO 14000 series of standards) during the development of their respective standards, to ensure that the level of compatibility is maintained or enhanced.
A recent review of ISO 14001 and ISO 14004 by ISO/TC 207/SC 1 has led to the initiation of a revision of these standards, which is targeted for completion by the end of 2004. This has provided an opportunity for further enhancement of the "compatibility" between the ISO 9000 and ISO 14000 standards.Are there any guidelines covering joint implementation of ISO 9001 and ISO 14001?
ISO has just initiated a project to prepare a guideline on this subject at this present time (January 2004). This will take account of the revision to ISO 14001, due towards the end of 2004.
For guidance on the auditing of both quality and environmental guidance management systems, the two responsible ISO technical committees (ISO/TC 176 and ISO/TC 207) jointly developed a single common auditing standard (ISO 19011) that replaced their own unique sets of auditing standards.
Is there a common guideline standard for auditing QMS and EMS according to ISO 9001 and 14001?
ISO 19011:2002 Guidelines for quality and/or environmental management systems auditing gives guidance on auditing that is applicable to both quality management systems and environmental management systems. [FAQ 043, April 2004]
How are the standards applicable to organizations that provide services?
The standards are applicable to all types of organizations, operating in all types of sectors, including service providers. (Note: the definition of the term 'product' in ISO 9000:2000 also includes 'services'. ISO 9001:2000 and ISO 9004:2000 have been written to reflect this definition.)
What do quality management practitioners (consultant, auditor, or trainer) need to know about the standards?
As a minimum, quality management practitioners should familiarize themselves with the requirements of ISO 9001:2000, and also with the content and philosophies of ISO 9000:2000, ISO 9004:2000 and the Quality Management Principles. They should understand their client’s activities and processes, before providing appropriate interpretations of the requirements of the standards, to add value to the client's operations. ISO/TC 176 is currently developing ISO 10019, Guidelines for the selection of quality management system consultants and use of their services, which may be useful to refer to for further guidance.How should regulatory bodies use the standards?
Regulatory bodies should review their regulations currently in effect (or under development) and identify points where reference to the quality management system standards would be appropriate, before making recommendations to the legislative body.
What do auditors need to know about the standards?
Auditors, whether external or internal, should be able to demonstrate their competence on the structure, content and terminology of the standards, and also on the underlying Quality Management Principles.
The standards require that auditors are able to understand the organization's activities and processes and appropriately audit against the requirements of the ISO 9001 in relation to the organization's objectives. According to joint advice from the International Accreditation Forum (IAF), ISO's Policy Committee for Conformity Assessment (ISO-CASCO) and ISO TC 176, auditors should be able to demonstrate competency in:
The requirements of the ISO 9001:2000.
The concepts and terminology of the ISO 9000:2000.
The eight Quality Management Principles
A general understanding of the performance improvement guidelines of ISO 9004:2000
Familiarity with the auditing guidance standard ISO 19011.
A recent initiative between ISO/TC 176, ISO/CASCO and the IAF has been the establishment of an ISO 9001 Auditing Practices Group, which has issued a number of web based guidance notes to assist auditors.
Benchmarking (also "best practice benchmarking" or "process benchmarking") is a process used in management and particularly strategic management, in which companies evaluate various aspects of their business processes in relation to best practice, usually within their own industry. This then allows companies to develop plans on how to adopt such best practice. Benchmarking may be a one-off event, but is often treated as a continuous process in which companies continually seek to challenge their practices.
A process similar to benchmarking is also used in technical product testing and in land surveying. See the article benchmark for these applications.
No comments:
Post a Comment